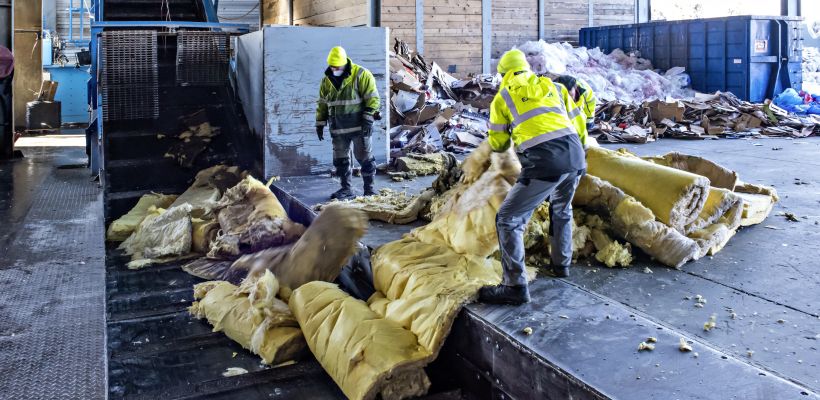
L'intégration de matériau recyclé dans la chaîne de production réduit l'emprunte carbone du produit.
Pour respecter les exigences nationales et européennes en matière de décarbonation des produits et matériaux de construction, la définition des moyens d’action en est évidemment une des clés de voute (avec leur financement on s’en doute). Dans le bardage, malgré la diversité des matériaux des parements, des systèmes d’ossature et des isolants, deux pistes sont néanmoins particulièrement explorées par les fabricants interrogés : l’amélioration des performances énergétiques et la circularité des matériaux. Avec une nécessité de cumuler les deux pour aboutir à un résultat suffisant.
Technologies
La substitution des énergies fossiles par une énergie décarbonée avance à des rythmes différents selon les activités industrielles. Ainsi, si chez le fabricant d’isolant Isover, son expert produit Jérôme Goudard rappelle qu’« en France, 100 % de nos fours de production de laine de verre fonctionne à l’électrique depuis plus de 10 ans », d’autres sont encore dans phase de l’intention. Chez Wienerberger (terre cuite), « les usines, qui ne sont pas localisées en France, fonctionnent au gaz naturel. Nous allons de le remplacer par du biogaz. Cette évolution permettra de réduire de 80 % les émissions de GES », souligne Gérald Merlin, chef de marché activité structure et façade. Idem chez Myral qui se penche sur l’électrification du chauffage de son conformateur.
« L’une des conditions pour que l’acier puisse être considéré comme bas carbone, c’est l’association de deux technologies, rappelle Prisca Lopez Voeltzel, responsable prescription grands comptes nationaux au sein d’ArcelorMittal Construction France : le recours à un four à arc électrique alimenté par de l’énergie solaire et / ou éolienne et la réduction directe à l’hydrogène. » Le groupe a notamment investi dans une usine permettant de combiner les deux solutions à Sestao en Espagne.
Matériaux recyclés
Le second levier clairement identifié, soit, on l’a vu, l’intégration de matériaux recyclés dans le process de fabrication, rentre plus concrètement dans les mœurs. « ArcelorMittal Construction France intègre depuis plus d’une décennie 20 % d’acier recyclé dans l’ensemble de ses produits d’enveloppe métallique, rappelle Prisca Lopez-Voeltzel. En outre, c’est le deuxième impératif pour produire de l’acier bas carbone : il doit contenir a minima 75 % d’acier recyclé », rappelle Prisca Lopez Voeltzel. C’est ainsi que l’acier XCarb « de sources recyclées et renouvelables », comme nomme ArcelorMittal sa gamme décarboné fabriquée à Sestao, est considérée comme telle car elle associe four à arc électrique + réduction directe à l’hydrogène + acier recyclé.
Chez Myral, 70 % des émissions de GES émanant des matières premières (elles-mêmes responsables de 90 % des émissions des produits fabriqués) sont générées par l’aluminium, 20 % par le polyuréthane et 10 % par le PVC. « Notre stratégie de décarbonation s’est rapidement orientée vers le choix de matières premières exerçant moins de pression sur les ressources naturelles, indique Julien Bagnard, directeur du groupe. Dans ce cadre, nous avons évalué les gains obtenus grâce à l’utilisation de matériaux issus du recyclage. » Quelques exemples : d’après les chiffres de l’industriel, fabriquer un parement aluminium avec 75 % de déchets post consumer économiserait 5,95 kg CO2e.m². Pour des rives PVC avec 50 % de PVC d’origine recyclé, c’est 0,811 kg CO2e.m². « Aujourd’hui, de manière générale, nos produits contiennent 50 % de matériaux recyclés. » Pareil chez Isover, « avec même des pointes à 80 % pour certains », indique Jérôme Goudard.
Gisements
Si le recours au recyclage semble couler de source pour limiter les émissions de GES, il dépend néanmoins de la disponibilité de gisements de qualité. Du côté de Myral, « nos sources diffèrent évidemment selon le matériau. Pour chacun d’eux, nous avons conclu des partenariats avec des entreprises spécialisées, précise Julien Bagnard. Ainsi, l’aluminium que nous récupérons dispose d’une certification garantissant 75 % de matériaux issus du recyclage de produits de consommation courante (canettes en aluminium par exemple). Pour la mousse isolante, c’est 15 % de PU recyclé, essentiellement issu de bouteilles PET. Enfin, 50 % du PVC provient de fenêtres, issues de la déconstruction ou de déchets propres à notre fournisseur. »
Mais que se passe-t-il lorsqu’utiliser des matières premières issues du recyclage n’est pas possible, faute de filière ou de solution technique ? C’est le cas par exemple de la terre cuite. « L’argile peut être réintroduite dans le process de production à condition qu’elle soit crue, signale Gérald Merlin. Lorsqu’elle est cuite, l’opération est plus complexe. » Il est possible de la concasser pour la réintégrer mais dans de faible proportion. « Un taux entre 1 et 3 % permet de jouer le rôle de dégraissant pour une argile moins collante. » Wienerberger privilégie plutôt le choix d’argiles issues de carrières de proximité et contenant le moins de calcaire possible. « A la cuisson, celles-ci sont moins émissives en CO2. » Le fabricant mise aussi sur le travail autour de l’éco-conception et la quantité de matière contenue dans le produit par « l’optimisation du design et de la géométrie. Il faut trouver le juste équilibre pour ne pas en diminuer les caractéristiques de résistance, de durabilité et d’esthétisme ».
Tests et essais
C’est en effet un point clé : les produits contenant des matériaux issus du recyclage ou à la conception différente ne doivent pas perdre en qualité. D’où la réalisation de tests et d’essais pour garantir l’équivalence avec le produit « classique ». « Les isolants concernés ont fait l’objet de tests de validation portant sur la résistance au feu, les performances acoustiques et thermiques, ainsi que sur leur mise en œuvre », précise Jérôme Goudard. Pour l’acier, « c’est notamment l’une des missions du Centre technique industriel de la construction métallique (CTICM) pour la filière », précise Hervé Gastaud, délégué général du syndicat de la construction métallique de France (SCMF). De manière plus générale, les industriels interrogés sont unanimes : « Ces opérations ont montré que les performances étaient identiques, voire meilleures », affirme Julien Bagnard. Un constat partagé par Prisca Lopez-Voetzel : « Il n’y a pas de différences entre un produit d’enveloppe fabriqué avec un acier issu de technologies traditionnelles et un produit d’enveloppe fabriqué avec un acier dit « bas carbone ». La résistance et les performances restent identiques » souligne la responsable prescription grands comptes nationaux. Idem pour le mode de mise en œuvre. Les Avis techniques ont été mis à jour pour les intégrer, sans modification du domaine d’emploi, « afin de rassurer les entreprises de pose et les assureurs », souligne la responsable prescription grands comptes nationaux. Pour les systèmes isolants en revanche, « nous avons recommencé les démarches de certification Acermi », rappellent Julien Bagnard.
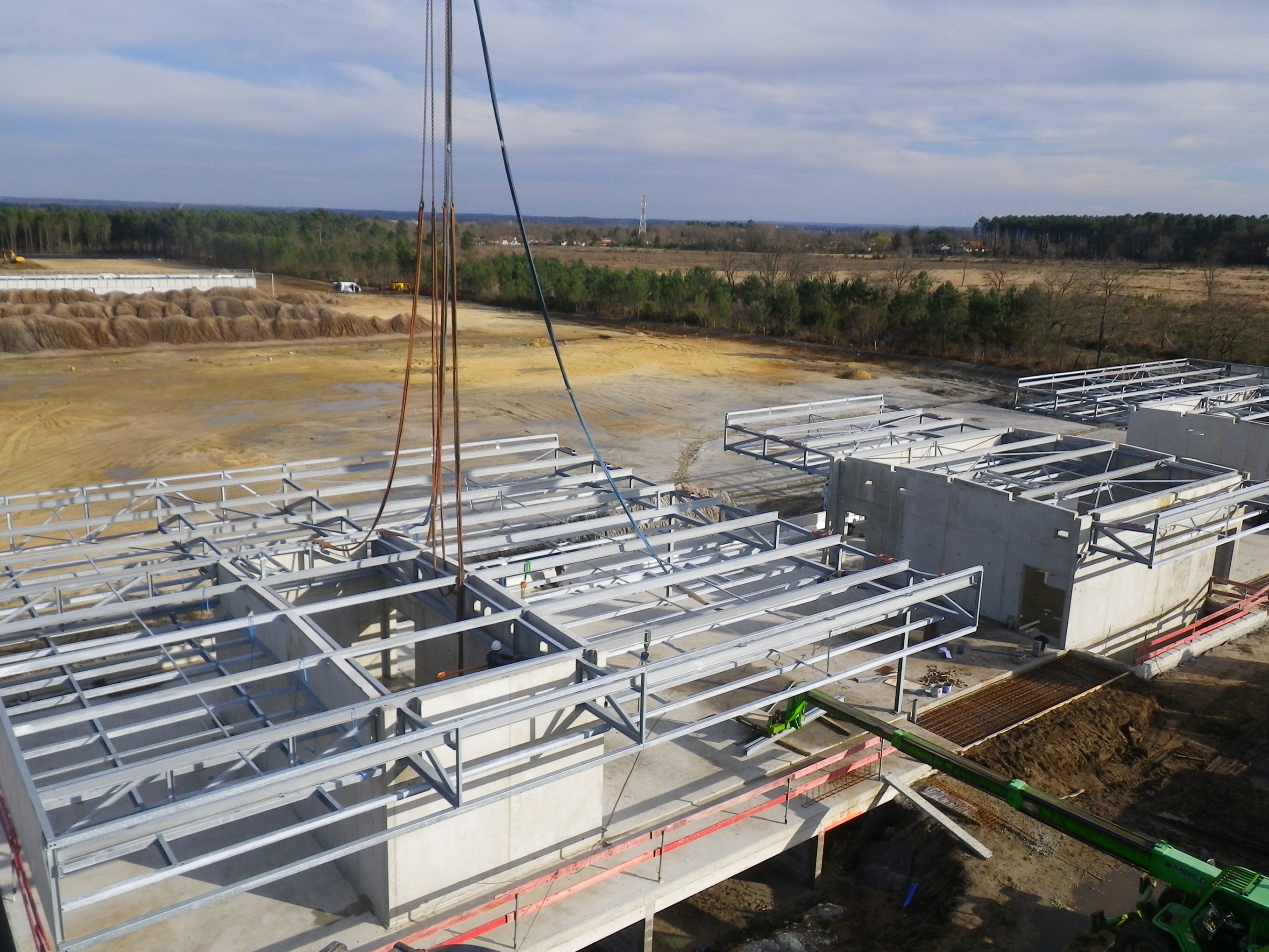
L'acier est recyclable à l'infini.
Parmi les autres leviers également exploitables pour réduire l’impact carbone des produits et procédés, on peut citer la récupération de chaleur fatale émise en sortie de four qui, comme par exemple chez Wienerberger, est réinjectée dans les séchoirs ou encore, toujours chez le fabricant de produit en terre cuite, la sélection d’engobe et d’émaux au faible impact carbone pour composer les pigments. Chez ArcelorMittal Construction France, une ligne de prélaquage sur Contrisson (55) est équipée depuis un an de l’EBT (Electron Beam Technology), une technologie pionnière soutenue par le Fonds Européen pour l’innovation, qui permet notamment d’utiliser une peinture sans solvant garantissant l’absence d’émission de COV, et au séchage quasi immédiat « En un an, nous avons déjà réduit de 20 % les émissions de CO2 par rapport à l’application d’une peinture classique. Nous prévoyons une économie de 35 000 tonnes en 10 ans », souligne Prisca Lopez-Voeltzel.
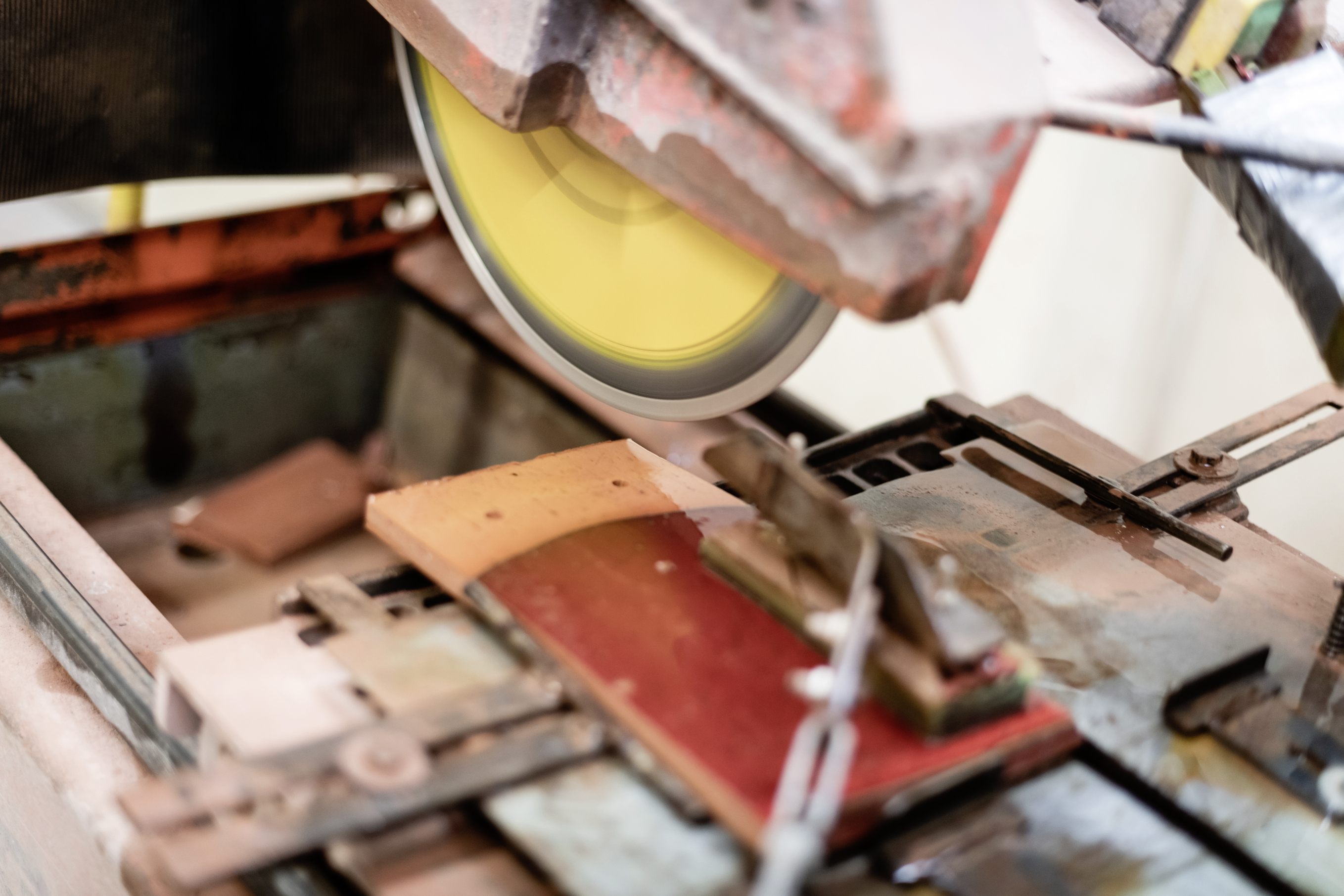
(c) GrégoryTachet
Pour réduire l'emprunte carbone de la terre cuite, l'optimisation du design et le choix des pigments peuvent jouer.
Transport et logistique
L’approvisionnement en matières premières locales, lorsqu’il est possible, joue lui aussi mais cette fois sur le transport. C’est en partant de ce constat par exemple qu’Isover a choisi l’implantation de ses usines. De manière générale également, les industriels ont développé un maillage territorial à même de limiter les distances entre zone de production et de stockage et leur clientèle. Les camions à vide sont proscrits et passent progressivement à l’électrique ou au biocarburant, tout comme, de plus en plus, les véhicules des collaborateurs. « Nous avons également recours aux solutions de transport intermodal route + train sur la ligne Orange – Avignon-Paris », ajoute Jérôme Goudard. Chez Faynot, on privilégie, « l’éclairage naturel et le passage au tout LED », décrit Stéphane Lambert, son responsable bureau d’études et normalisation, également président du Syndicat national des bardages ventilés isolés (SNBVI).
- 2,1 % entre 2015 et 2022
Au final, l’impact de toutes ces mesures est-il réel ? Oui ! répondent évidemment les industriels, chiffres à la clé. Ainsi, selon Myral, le bilan carbone mentionné dans la FDES de son système de façade a baissé, passant de 39 kg de CO2 à un peu moins de 21 kg. Les parements et profils de bardage décarbonés d’ArcelorMittal Construction affichent, quant à eux, un poids carbone inférieur de 54 % par rapport aux gammes classiques.
C’est encourageant mais pas suffisant. Selon le cabinet de conseil sur les enjeux énergie et climat Carbone 4, les émissions des industries de la construction et des minéraux métalliques de la construction ont diminué de 2,1 % entre 2015 et 2022 alors que la SNBC 2 en attendait 19 % (-2,6 % par an). Il faut donc aller plus loin. En France, par exemple, les hauts-fourneaux de Dunkerque et de Fos-sur-Mer d’ArcelorMittal restent alimentés au charbon.
Les process de fabrication moins carbonés doivent être généralisés et sortir du cadre de la réflexion ou de l’expérimentation dès que possible. Des pistes comme le captage du CO2 restent encore à approfondir. La relocalisation de certaines productions en France pourrait également avoir un effet comme le souligne, entre autres, la Direction générale des entreprises, rattachée au ministère de l’économie et des finances : « la baisse des émissions directes s’est accompagnée d’une hausse des émissions liées aux importations, même si une réduction de l’empreinte carbone est observée depuis plusieurs années. » Il y a encore de la route à faire.
Retrouvez la première partie de notre dossier "Décarbonation : agir aujourd'hui pour l'industrie de demain" en cliquant ici.