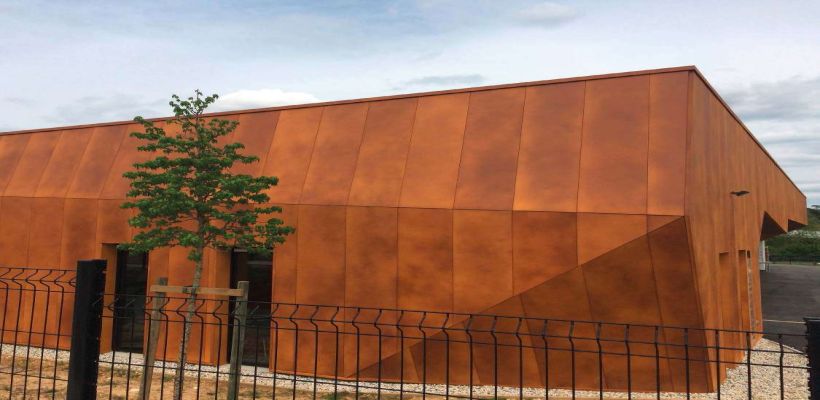
L'appellation bardage double peau définit, de manière générique, l'ensemble des procédés de façade métallique intégrant un plateau, une épaisseur d'isolant, d'éventuels écarteurs (voir encadré) et un parement d'habillage. Arrivés en France dans les années 1960, les procédés cumulent alors les avantages dans une France en plein essor économique. Avec leurs panneaux extérieurs en tôles, ils combinent faible coût, légèreté et rapidité de mise en œuvre. Leur principal débouché : les ouvrages industriels, un secteur où l'esthétique et les performances thermiques ne sont pas encore des préoccupations. À l'époque, la fonction première de l'isolation reste en effet la maîtrise des phénomènes de condensation. Les épaisseurs d'isolant mises en œuvre sont réduites au minimum et ne dépassent guère les 45 mm. À partir de 1974, le renforcement continu des réglementations thermiques change peu à peu la donne.
Les procédés de bardage double peau évoluent progressivement pour afficher aujourd'hui des performances thermiques en adéquation avec les textes réglementaires mais également des niveaux de résistance et de durabilité améliorés. Le tout notamment grâce aux progrès réalisés en matière de fixations. Par exemple, dès 1975, l'arrivée de la vis autoperceuse sonne le glas de la pince à crever. La pose devient plus rapide et surtout moins chère.
RÉDACTION DE RÉFÉRENTIELS
En 1978, un premier texte visant à encadrer les pratiques voit le jour avec la publication des « Recommandations professionnelles pour la fabrication et la mise en œuvre des bardages métalliques ». Elles sont remplacées trois ans plus tard, par une deuxième version mise à jour. « Ce document a longtemps représenté la Bible de la mise en œuvre des bardages double peau », rappelle Pierre Archez, dirigeant de l'entreprise de bardage Ogim. Il intègre l'annexe B dédiée aux « conditions minimales imposées aux fixations pouvant être utilisées pour la mise en œuvre des bardages métalliques ». Type de fixations, dimensionnement, domaine d'emploi, protection contre la corrosion sont ainsi renseignés.
Sur le terrain pourtant, les exigences croissantes en matière de performances énergétiques des parois et de durabilité des procédés poussent les professionnels à s'affranchir peu à peu des instructions décrites dans le référentiel. Les épaisseurs d'isolant augmentent, les matériaux rapportés se diversifient, le bardage devient étanche à l'air (voir encadré). Si bien qu'en 2014, pour ne plus laisser place à l'improvisation, le programme RAGE rédige ses Recommandations professionnelles (RP) « Bardage en acier protégé et en acier inoxydable ». Elles réunissent, pour la première fois dans un même document, les techniques pratiquées depuis plus de 20 ans.
PROTECTION CONTRE LA CORROSION
Éléments essentiels de la tenue du procédé, les fixations tiennent une place de choix dans le nouveau référentiel. L'annexe qui leur est consacrée actualise et renforce les obligations à respecter. Elle insiste particulièrement sur la protection à la corrosion des fixations, avec des niveaux imposés bien supérieurs aux exigences du précédent référentiel. Elle précise que « les systèmes de fixation doivent être choisis de façon à permettre une tenue à la corrosion du bardage égale ou supérieure à celle des éléments qu'ils assemblent. » Ces obligations, détaillées dans une série de tableaux en fonction du support et du type de fixation, distinguent également les différents composants de la fixation : corps, tête, collerette « Les Règles professionnelles de 1981 n'exigeaient généralement qu'un électrozinguage. Désormais, par exemple, une tête de vis exposée à l'atmosphère extérieure doit être de nature à résister aux intempéries, par exemple, par le sertissage d'une feuille d'acier inoxydable », précise Flavien Rousset, chef de produit couverture, bardage et étanchéité pour le fabricant de fixations SFS. Quant au corps, il doit présenter une résistance minimale de 12 cycles Kesternich, méthode d'essai consistant à créer une atmosphère saturée en humidité et chargée en dioxyde de soufre. « L'ensemble de la fixation sera également adapté au matériau de l'élément du bardage à fixer afin d'éviter tout risque de couple galvanique incompatible », insiste David Piantino, directeur études et développement du groupe Lagarrigue.
De la même manière, les RP RAGE ont amélioré les prescriptions dimensionnelles. Le précédent document ne précisait pas les caractéristiques minimales des vis autoperceuses, à part en cas de support en métal. Désormais, les diamètres minimum des fixations sont de 4,8 mm sur les opérations de couturage de plateaux, 5,5 mm pour un liaisonnement sur support en métal et 6,3 mm sur support bois.
En revanche, les types de fixations qui ne permettent pas de répondre à l'ensemble de ces nouvelles contraintes ne sont aujourd'hui plus visés par les Recommandations professionnelles. C'est le cas des rivets pour la fixation de l'enveloppe extérieure ou des clous à percussion pour les plateaux perforés. Ils sont autorisés sous condition que le plateau soit plein et le clou sous Avis technique.
SUR LE TERRAIN
Aujourd'hui, tous les fabricants de fixations ont évidemment adapté leurs produits aux Règles de l'art. « Ils sont soumis à toute une batterie de tests et d'essais vérifiant leurs caractéristiques, conformément aux normes d'essais de la série NF P30-31X », précise Stéphane Lambert, responsable BE et normalisation pour Faynot.
Pour chaque chantier, leur choix relève de la responsabilité de l'entreprise de pose, selon la configuration de l'ouvrage. En plus des niveaux de résistance à la corrosion, définis selon les atmosphères extérieures et ambiances intérieures du bâtiment, plusieurs critères sont à prendre en compte. Tout d'abord, le support et son épaisseur détermineront le type de fixation : vis à bois ou tirefond en cas de charpente bois, pistoscellement ou vis autoperceuse en cas de charpente en acier et couple insert métallique / vis pour les supports béton. « Pour la fixation des plateaux à la charpente métallique, nous avons recours aux clous à frapper lorsque les poteaux supports présentent une épaisseur supérieure à 6 mm », explique Pierre Archez. « Ils sont appliqués par pistoscellement avec un pistolet à poudre dont la puissance est déterminée par rapport à l'épaisseur de la charpente », précise Pascal Pro-fichet, directeur façades chez Hilti. Pour couturer les plateaux ou les tôles de bardage laquées, la vis autoperceuse convient parfaitement, sous réserve de choisir une fixation à capacité de perçage adaptée aux tôles minces, avec un petit diamètre de foret, une pointe pilote et une longueur suffisante. Par ailleurs, pour fixer la peau extérieure, comme l'explique Philippe Tolleret, directeur technique chez Etanco, lorsque l'isolant est déroulé devant les lèvres de plateau, « la vis doit également présenter une capacité d'assemblage suffisante avec une longueur filetée supérieure à la somme des épaisseurs des tôles et de l'isolant comprimé. » En veillant à ce que ce dernier ne soit pas trop compressé.
En effet, « cela génèrera des ponts thermiques à prendre en compte pour le calcul du coefficient de transmission thermique U », précisent les RP. Le risque étant de s'éloigner des exigences de performances énergétiques actuelles.
MISE EN ŒUVRE
Pour l'éviter, l'usage d'outils adaptés aux produits est tout aussi important que le produit lui-même. « Afin de prévenir un serrage trop important et donc un mauvais fonctionnement de la rondelle d'étanchéité, la pose de vis autoperceuses nécessite le recours à une visseuse de bardage associée à une butée de profondeur. De plus, l'utilisation d'une visseuse type «visseuse à chocs» pourrait affaiblir la fixation », explique Flavien Rousset. C'est pourquoi les visseuses à chocs sont interdites pour ce type d'application. Elles pourraient notamment réduire la tenue des fixations aux efforts mécaniques subis du fait du vent, des actions sismiques, du poids propre au bardage etc. « Les efforts sont repris et transmis de la fixation vers l'ossature ou le plateau. Elle doit donc afficher un niveau de résistance caractéristique à l'arrachement (P ) et au déboutonnage adapté à la configuration du procédé, de l'ouvrage et de son environnement », souligne Sébastien Charton, responsable du service technique produit et innovation chez ArcelorMit-tal Construction France. Cette valeur, fournie par le fabricant, sera intégrée dans les calculs vérifiant la bonne conception du système. Elle pourra également compléter, le cas échant, les préconisations de densité de fixations décrites dans les RP (voir encadré) en fonction des efforts de vent. C'est le cas par exemple, pour la détermination du nombre de vis autoperceuses destinées à la fixation de la peau extérieure ou des écarteurs. À noter que pour le liai-sonnement des plateaux sur support métallique ou bois, « afin d'accroître les surfaces de répartition et réduire le risque de déboutonnage, il est recommandé d'utiliser des vis autoperceuses à collerettes larges (15 mm) ou des plaquettes de répartition, notamment sur plateaux perforés », ajoute Laurent Guillotel, chef de produits bardage et étanchéité chez Etanco.
PROCÉDÉS SOUS AVIS TECHNIQUES
Les RP RAGE constituent le référentiel applicable aux procédés de bardage double peau entrant dans le spectre de la traditionnalité. D'autres, développés par deux industriels de l'isolation (Rockwool avec Rockbardage et Isover avec Cladi-sol), sont validés par Avis techniques, complétés, le cas échéant, par le e-cahier du CSTB n° 3780 « Conception et mise en œuvre des pare-pluie métalliques et plateaux métalliques destinés à recevoir un procédé de « bardage rapporté fixé par vis entretoises sur plateaux métalliques » bénéficiant d'un Avis technique ». Lancés dans les années 2000, ils visent à réduire encore les ponts thermiques. Le principe : supprimer les contacts entre le plateau et la peau extérieure. Pour cela, « le panneau isolant positionné en fond de plateau est plus épais que la largeur des lèvres, ce qui lui permet de les recouvrir et de supprimer cette source de déperdition énergétique », décrit Céline Florence, chef de projet développement bardage pour Rockwool. L'entretoise peut atteindre 40, 60 et même 80 mm depuis décembre 2017 pour certains procédés. Pour éviter leur compression, les rives longitudinales des panneaux isolant sont façonnées de manière à épouser la géométrie spécifique des lèvres et des ailes du plateau. Résultat, « avec une seule épaisseur d'isolant, la performance globale de la paroi est supérieure à celle des systèmes traditionnels. Sans oublier que les temps de pose sont également optimisés », souligne Nicolas Bretault, responsable marketing client chez Isover.
« Au sein des systèmes à entretoise, le maintien d'un espace suffisant entre les lèvres de plateau et la peau extérieure est assuré par des vis spécifiques. »
Le maintien d'un espace suffisant (donc de 40, 60 ou 80 mm) entre les lèvres de plateaux et la peau extérieure est assuré par la mise en œuvre de vis spécifiques. « Ces vis autoperceuses sont équipées d'un filet dissymétrique sous tête et d'une butée qui assurent cette fonction d'entretoise », explique le directeur technique et du co-développement chez Etanco. Ce système de fixation autorise aussi bien le liaisonnement de bardages verticaux qu'horizontaux avec interposition d'écarteurs. Mais si l'entretoise permet d'améliorer les performances thermiques, ce ne doit pas être au détriment de la stabilité du parement extérieur. « La reprise de la charge verticale est assurée par le fonctionnement conjoint des vis et de la bonne tenue mécanique des panneaux isolant », rappelle Céline Florence. D'où l'importance de vérifier auprès du fabricant les qualités de la fixation en la matière et, le cas échéant, sa référence dans l'Avis Technique concerné.