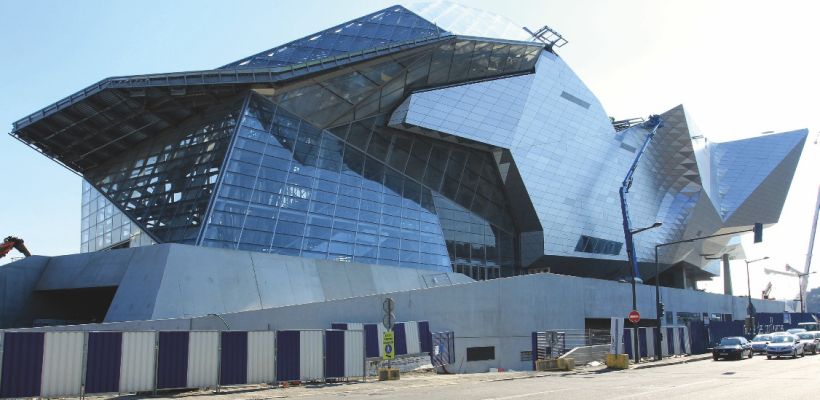
Situé à la confluence de la Saône et du Rhône, le nouveau musée des sciences et des sociétés métamorphose l’entrée sud de la ville de Lyon.
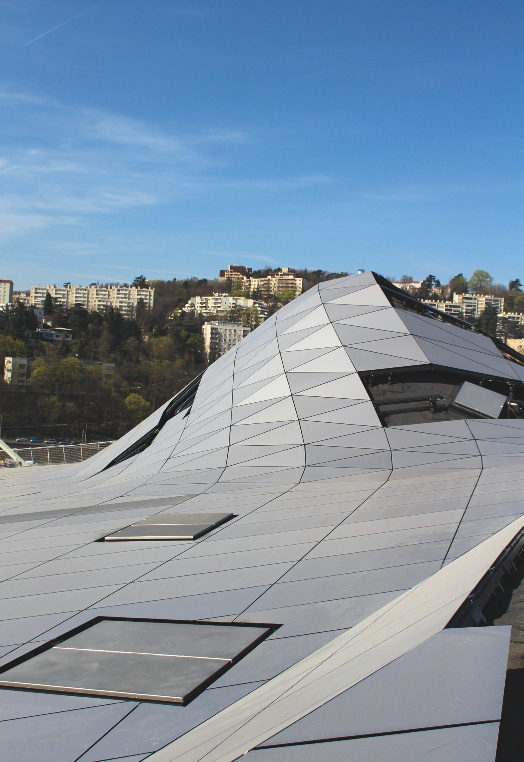
© Pyc
Le Nuage, composé de 13 000 panneaux en inox, prend la forme d’un vaisseau spatial.
Plus de 10 ans auront été nécessaires pour venir à bout de la construction du musée des Confluences de Lyon, dédié aux sciences et sociétés. Le chantier, lancé en 2001, est aujourd’hui en passe de s’achever et l’ouverture au public est prévue pour la fin de l’année. En attendant, il offre déjà au sud de Lyon une entrée monumentale. « Sa localisation, à la confluence entre le Rhône et la Saône, nous a inspiré un ouvrage d’une surface de 40 000 m² superposant, sur un socle de béton de 8 m de hauteur, deux unités architecturales complexes reliées entre elles : le cristal et le nuage », expliquent les architectes de l’agence Coop Himmelb(l)au. Le premier (61 m de long, 35 m de large et 36 m de haut) fait face à la ville et recevra les visiteurs. « Formé de vitrage transparent, il est conçu comme une place. » Le second accueillera les salles d’exposition. Il mesure 150 m de long, 83 m de large et 37 m de haut et « ressemble à un vaisseau spatial momentanément arrêté dans le temps et l’espace ». 13 000 plaques en acier inoxydable de 3 mm d’épaisseur et d’aspect microbillé composent le pare-ment des 12 000 m² d’enveloppe, mis en œuvre sur une charpente métallique par l’entreprise de bardage Smac, en charge, entre autres, du lot (voir encadré).
Procédé breveté
Environ la moitié de cette surface est traitée à la ma-nière d’une sur-toiture liaisonnée à l’élément porteur et au complexe d’étanchéité bicouche bitumineuse soudé en plein sur un isolant en laine de roche sur-facée. Connecté à la charpente par des écarteurs, l’élément porteur en bacs acier nervurés est associé, en sous-face, à un procédé thermo-acoustique (pla-teau + pare-vapeur + isolants) positionné direc-tement sur la charpente. L’intégralité du système, conçu pour cet ouvrage, assure un affaiblissement acoustique Ra,tr = 53 dB et une résistance ther-mique Up = 0,18 W/m².K pour une épaisseur de 46 cm. La sur-toiture est fixée à l’ensemble grâce à un procédé spécifique développé par Smac (voir encadré), composé de platines en inox connectées aux bacs acier à travers le complexe d’étanchéité. Des plastrons viennent assurer l’étanchéité de ces platines. « Ce système, mis en œuvre après la pose des membranes, permet une mise hors d’eau rapide du bâtiment. Les corps d’état intervenant à l’intérieur de l’ouvrage peuvent ainsi avancer leurs travaux simul-tanément à l’installation de la sur-toiture », précise Bruno Laforge, chef de projet chez Smac. Sur les platines sont ensuite rapportés, par l’intermédiaire d’étriers, des porteurs en aluminium réglables supports des parements en inox. Ces derniers sont équipés, en sous-face, d’un système de fixations invisibles par ossatures métalliques.
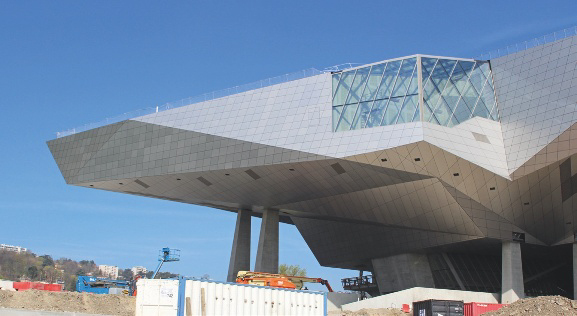
© Pyc
Lorsque la pente est trop importante, le parement est liaisonné à la toiture par un système de potelets à tête pivotante.
Mais ce procédé a ses limites. Lorsque la charpente de la toiture présente des reliefs avec une pente su-périeure à 30 °, les platines ne suffisent plus pour as-surer les reprises de charges tangentielles. « Dans ces cas de figure, nous avons eu recours à des pote-lets traversant jusqu’à la charpente. Ils sont tous dotés d’une tête spécifique réglable selon les trois axes afin de positionner et de régler précisément les porteurs en fonction de la forme souhaitée par l’architecte. »
Bardage simples et double peau
La charpente métallique tout comme les parements en inox se prolongent en façades formées par des blocs de béton cellulaire lorsque la surface est plane (au sud et à l’est). C’est alors un système classique de bardage simple peau qui constitue l’enveloppe. « Les porteurs en acier plié réglables des panneaux sont liaisonnés aux profils de la charpente par des étriers », indique Bruno Laforge. Côté ouest en revanche, les courbes et les variations d’inclinaison des 1 700 m² de façade ont imposé la mise en œuvre d’un système de bardage adapté qui devait également participer au guidage de l’eau vers le réseau d’évacuation des eaux pluviales.
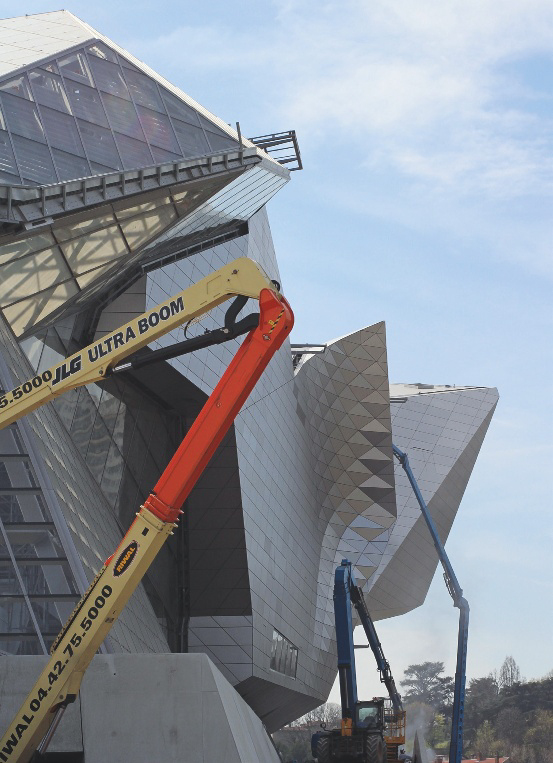
© Pyc
Une quinzaine de nacelles élévatrices ont été nécessaires pour traiter les 12 000 m2 de l’enveloppe.
« Nous avons eu recours à des bacs supports, associés à une isolation de 40 mm d’épais-seur revêtue d’une étanchéité monocouche soudée en plein, et à une autre technique spécifique développée par Smac : les profilés drainants. Ces derniers sont rapporté tous les 1,10 m. L’eau qui s’infiltre par les trous de fixations est canalisée par le profil jusqu’à son extrémité ouverte. Les profils étanchés servent également de support aux porteurs de parements. » Pour épouser fidèlement les reliefs, les plateaux ont été découpés en trapèze. De plus, les réglages de la charpente métallique n’ayant pas été effectués aussi précisément que prévu, « nous avons fait appel à quatre géomètres pour positionner et ajuster nos porteurs de bardage afin de rattraper ces tolérances ».
Nacelles
Pour mettre en œuvre l’ensemble de ces 12 000 m² de façade et de sur-toiture, jusqu’à quinze nacelles élévatrices différentes ont été mobilisées. La plus grosse pouvait monter jusqu’à 43 m. « Nous avons même fait fabriquer une machine spécifique proche de la nacelle araignée et équipée de palonnier à ventouse pour réaliser la colline inversée en sous-face du nuage, ajoute le chargé d’études. Nous pouvions ainsi trans-porter les plaques en inox comme des vitrages et nous déplacer dans les trois axes. »
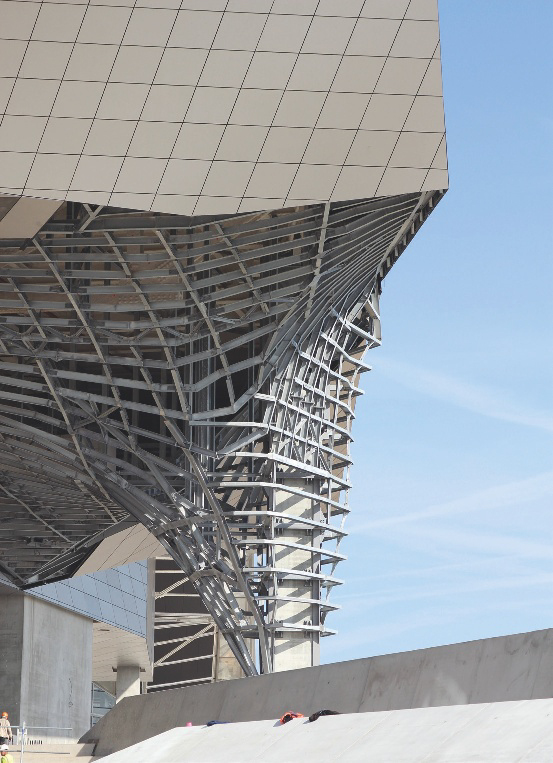
© Pyc
Le bardage est entièrement fixé à une ossature métallique.
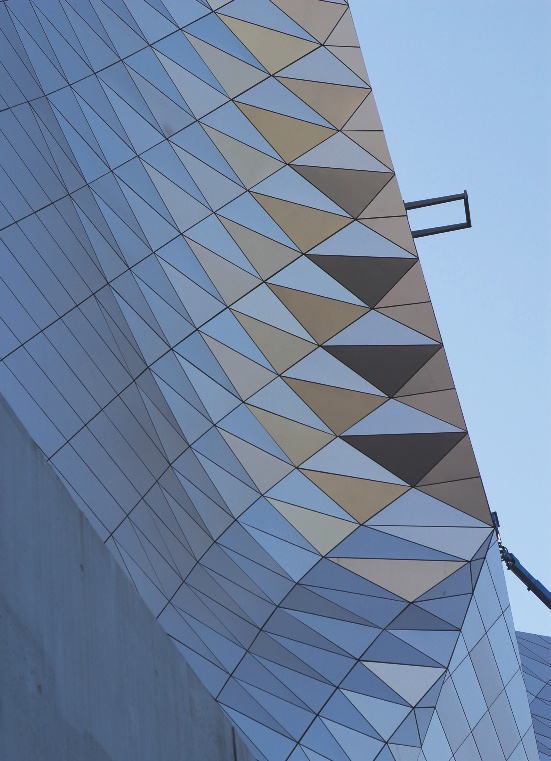
© Pyc
La fabrication de toutes les plaques inox a été réalisée à partir des plans 3D de l’architecte, sans prise de cote in situ.
Des parements fabriqués sur plan
Sur les 13 000 plaques mises en œuvre, un peu moins de la moitié ont une taille standard. La raison : le bâtiment
est coupé par différents plans qui changent l’inclinaison des parements et créent des arêtes. Les 7 000 panneaux positionnés en rive et à la jonction de deux orientations ont nécessité la réalisation de plans de fabrication spécifiques. « Nous ne pouvions absolument pas modifier le calepinage de l’architecte. L’ensemble des parements en inox a donc été fabriqué à partir des plans 3D de la maîtrise d’œuvre, sans prendre aucune cote sur place, explique Bruno Laforge. Pour répondre à l’ensemble des configurations de pose du chantier, nous avons créé treize filières spécifiques de fabrication. »