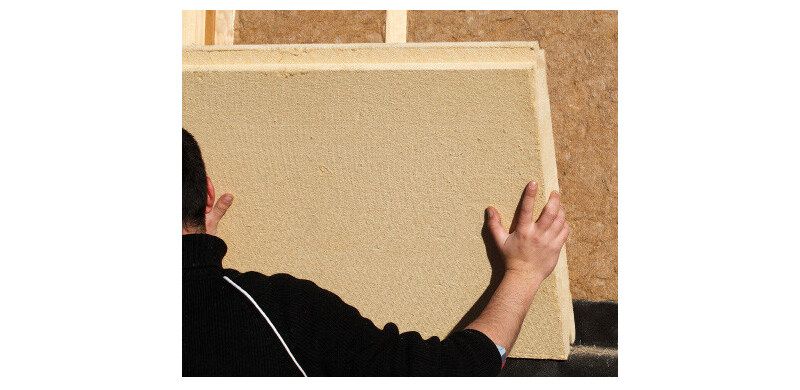
Les isolants biosourcés se déclinenten plusieurs formats.
L’isolation biosourcée a la cote et ça ne devrait pas s’arrêter là. Ainsi, selon l’Association des industriels de la construction biosourcée (AICB), depuis 2016, 130 millions de m² ont été mis en œuvre et la croissance du secteur a dépassé les 85 %. Il pèserait aujourd’hui pour 10 % du marché, avec 27 millions de m² posés en 2020. L’étude MSI Reports sur « le marché des produits d’isolation thermique dans le bâtiment en France » publiée en juillet 2020 a, quant à elle, évalué la hausse à plus de 15 % en surface et 16 % en volume entre 2018 et 2019, soit une croissance supérieure à celle du marché global des produits d’isolation thermique (+ 9% en surface et + 10,5 % en volume). Les projections pour les cinq prochaines années sont bonnes. « Les professionnels du secteur considèrent que le marché continuera à être très dynamique. »*
Des grands groupes industriels se positionnent
Boosté par ces perspectives alléchantes, le tissu industriel tend à se structurer. De nombreux acteurs sont apparus depuis dix ans. Beaucoup ont disparu depuis, notamment en raison de défaut de performance des produits. Ils sont aujourd’hui progressivement remplacés par de grands groupes industriels, bien décidés à se positionner sur ce segment d’avenir. C’est le cas d’Isover-Saint-Gobain, qui a racheté en 2016 le fabricant français d’isolants en fibres de bois Buitex Recyclage devenu depuis Isonat et Soprema qui a fait l’acquisition la même année du fabricant suisse de produits d’isolation thermique et acoustique Pavatex. Une quinzaine d’acteurs principaux se répartissent aujourd’hui le marché*.
Cette nouvelle assise industrielle génère des investissements dans les outils de production. Car devant la probable envolée de la demande, l’offre va devoir suivre. Déjà, « les commandes sont supérieures aux capacités des usines existantes », rappelle Blaise Dupré, directeur du centre de recherches isolant biosourcé d’Isonat. C’est pourquoi le groupe va doubler ses capacités de fabrication d’ici trois ans pour atteindre 40 000 tonnes chaque année. Idem chez Steico ou Pavatex qui augmentent le nombre de leurs lignes de production. En espérant, bien sûr, que la crise des matières premières qui touchent aujourd’hui les matériaux et notamment le bois, ne soit plus qu’un mauvais souvenir.
L’atout naturel
Comment expliquer cette tendance ? Le secteur profite tout d’abord de la croissance généralisée du marché de l’isolation, porté par le renforcement des exigences de performance énergétique, dans le neuf et en rénovation. Plus spécifiquement, il bénéficie d’arguments de poids dans le contexte actuel. D’origine naturelle, la filière biosourcée suscite l’intérêt croissant de particuliers et de prescripteurs de plus en plus sensibles à leur impact écologique. Depuis les confinements même, « la demande explose », insiste Blaise Dupré.
Elle tire également avantage de l’arrivée imminente de la RE2020 et du calcul des émissions de gaz à effet de serre des ouvrages. « Issus de ressources renouvelables ou recyclés, ils stockent le carbone et les process de fabrication sont peu émetteurs », rappelle Yves Hustache, associé fondateur du bureau d’études Karibati. Des points en plus pour les Fiches de déclaration environnementale et sanitaire (FDES) des produits et le calcul de l’impact carbone (IC) de l’ouvrage. Autre atout : la production est majoritairement locale. « Notre usine de production d’isolants biosourcés, basée à Roanne (42), n’utilise que des ressources accessibles dans un rayon de moins de 60 km, souligne Blaise Dupré. Pour le transport, nous bénéficions du soutien logistique de notre maison mère qui nous permet de remplir les camions avec un panaché de matériaux, biosourcés ou non, ce qui réduit donc à la fois les émissions de CO2 et les coûts. »
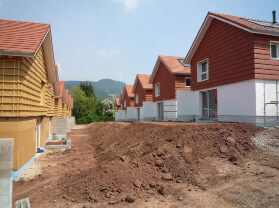
© Pavatex/UICB
« Les isolants biosourcés manquent de validation technique, ce qui complique les justifications auprès des assureurs. »
Encore des freins
Ces coûts justement sont supérieurs à ceux pratiqués dans l’isolation d’origine minérale ou plastique. Ce frein au développement est amplifié par les automatismes des entreprises, rodées aux laines minérales. Les habitudes sont d’autant plus difficiles à changer que le recours à ces produits manque encore, selon les usages, de validation technique et complique la justification des systèmes auprès des assureurs. C’est particulièrement le cas en bardage rapporté. Si certains matériaux sont visés par des NF DTU (comme la ouate de cellulose dans le NF DTU 45.11 « Isolation thermique de combles par soufflage d’isolant en vrac, (laines minérales ou ouate de cellulose papier) ») ou par des Règles professionnelles (comme par exemple la paille), aucune prescription technique relative au bardage ne mentionne les isolants biosourcés. Pas mieux dans les Avis techniques ou ATEx des produits. Résultat, leurs comportements au feu et à l’humidité sont encore mal connus. Le domaine d’emploi s’en retrouve restreint et la mise en œuvre demande des précautions particulières.
Confidentiel en bardage
Le marché des isolants biosourcés intégrés dans les systèmes de bardage rapporté reste donc encore confidentiel. 290 000 m² (exclusivement en panneaux de fibres de bois) ont été mis en œuvre en 2019, soit plus de quatre fois moins qu’en contre-cloison sur ossature (ITI) et près d’1,5 fois moins qu’en ITE sous enduit* bien mieux pourvus en documents de référence. Il se développe sur des petits bâtiments mais il sera nécessaire de déverrouiller ces points bloquants pour dynamiser la filière.
Les principaux matériaux pour l’isolation biosourcée
Parmi les natures d’isolants disponibles, la fibre de bois rigide ou semi-rigide domine clairement, avec 45 % des parts de marché en 2019. La ouate de cellulose vient ensuite avec 35 %, suivie du coton recyclé (un peu moins de 10 %) et du chanvre/lin (9 %) *.
- La fibre de bois : elle se présente essentiellement sous forme de panneaux rigides ou semi-rigides et dans une moindre mesure, en vrac, obtenus à partir de produits de scieries (copeaux, sciures…). Elle est admise dans sa version semi-rigide en isolation thermique par l’intérieur, l’isolation des combles perdus et des rampants de toiture. On la retrouve en ITE sous bardage rapporté dans son format rigide.
- La ouate de cellulose : fabriquée à partir de papiers neufs ou recyclés, elle s’utilise en panneaux (isolation par l’intérieur des murs et de combles perdus) ou en vrac par soufflage à sec (combles perdus), insufflation à secs dans des caissons (murs et planchers), projection humide (murs) et flocage humide (sous-faces de planchers).
- Le coton recyclé : les produits d’isolation à base de vêtements recyclés séduisent de plus en plus. Ils peuvent être conditionnés en panneaux semi-rigides pour l’isolation des murs, des combles perdus et des rampants de toiture. Sous forme de vrac, ils s’utilisent pour l’isolation des murs et des combles perdus.
- La fibre de lin et chanvre : disponible en laine souple, panneaux semi-rigides ou vrac, elle s’applique en isolation des murs, des combles perdus et des rampants de toiture.
- Le liège : les panneaux ou rouleaux de liège sont fabriqués à partir de l’écorce de chêne-liège ou de bouchons de liège. Ils peuvent isoler les planchers, les murs par l’intérieur ou l’extérieur, les combles perdus et les rampants de toiture.
- La paille : « après fauchage, la paille est en général conditionnée sous forme de bottes pouvant être utilisées telles quelles comme isolant dans une ossature bois », explique la Fédération française du bâtiment (FFB) dans son guide dédié aux matériaux biosourcés. Remplissage des murs, en toiture et isolation thermique par l’extérieur sont les trois domaines d’application possibles.
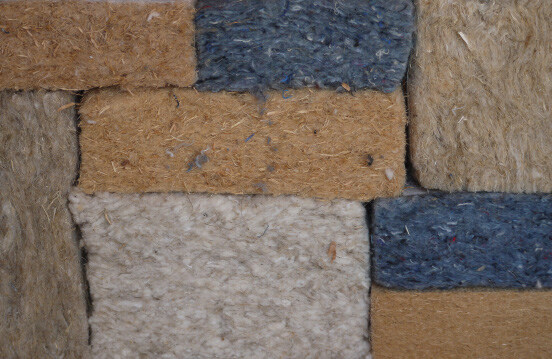
© Karibati
Plusieurs matériaux peuvent être utilisés pour l’isolation des bâtiments avec, parmi les plus courants, la fibre de bois, la ouate de cellulose et le coton recyclé.